『能率』にあけた人間の風穴
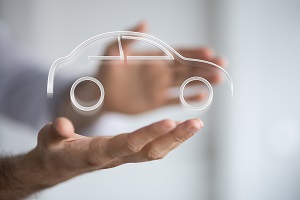
第15回 労使はこうしてトヨタをつくりあげた
「利益目標」という名の魔物
企業は利益をあげなければ存続できない。それは極めて当たり前のことであるが、だからといって、利益目標を個々の社員に割り当てて、それを目標に、社員を駆り立てるだけで「利益」を確保することは難しい。
なぜなら、利益は会社経営の結果に過ぎず、個々の社員の努力とそのまま比例するものではないからである。したがって、会社全体の「利益」目標を社員に割り当てるというようなことは、全員が営業マンである小さな販売会社でもない限りなされることはない。
仮に無理に製造現場に利益目標などを示すと、現場が苦し紛れに材料費を節約したりして、知らぬ間に品質が下がっていたというような事態が起こりかねない。
そこで利益に似たものとして、「売り上げ」や「生産台数」という、現場である程度管理可能な数字を目標として現場に課す企業は少なくない。これは、数字としてはっきりするものであるし、企業の目標ともリンクするからわかりやすいとも言える。
しかし、製造業においては、時に現場を苦しめることがある。なぜなら、売上も生産台数も、景気や製品の人気度合で増減するものであり、現場の努力だけではいかんともしがたい面があるからである。無理にこれで現場を締め付けると、従業員の反発を招き、モチベーションが下がる危険がある。
能率という目標
部署ごと、工場ごとに数値目標を与え、その変化(向上度合)を把握することは、企業にとって現場管理と同時に、その数値にインセンティブを付けることで従業員のモチベーションをあげることが可能だ。
その必要性は高いといえるが、どんな数字を掲げるかはなかなか難しい。
トヨタでは会社創成期である「生産基盤確立期」以来、現場を、「生産性」と「原価低減」という二つの数字のみで管理してきた。
具体的には、「生産性向上」は、現場ごとに生産するものの第1号で決めた製造必要時間を、日々の創意工夫と改善で短縮し、何人が何時間で作ったかという実績(投入工数)の低減具合で測る。
その割合は、給料にも反映される。また「原価低減」は、生産に用いる原材料、エネルギーなどを日々1銭単位で低減していく目標を定め、その達成度合いを評価する、ということである。これだと、会社の売り上げの好不調にかかわりなく、現場の努力のみで動かせる数字だから、納得性があるし、モチベーションにもつながる。
私は、産業別組織である自動車総連に行くまで、トヨタのやりかたしか知らなかったから、製造業では、呼び方こそ違え、こういう考え方が当たり前であると思っていた。
しかし、他のメーカーや部品メーカーに聞いてみるとそうではなかった。現場の努力だけでは達成しかねる数字を現場に目標として課している会社は意外に多かった。
「能率」という数字の怖さ
トヨタでは、車をモデルチェンジするたびに、全部品、車両について、製造工程における製造必要時間を測定し「基準時間」を決める。
基準時間が決まると、工程ごとに必要な人間の数も決まる。これでスタートした生産性を、現場の知恵と工夫で日々改善し、短縮していく。
その短縮度合が「能率」であり、その数字が良くなっていくことが、「生産性向上」である。現場にとって、自分たちが属す「課」の能率が上がることは、努力が実を結んでいることであるから嬉しいし、それがわずかながらでも給与にも跳ね返るということで、モチベーションも上がる。原価低減もそうである。
効率良く生産すればするほど、また、創意工夫で材料の歩留まりを良くすれば良くするほど原価は下がる。努力がそのまま数字に表れる。これも、現場を奮い立たせる「目標」となる。
しかし、この「能率」の怖いところは、分母(投入工数)の数字を小さくすることで、目に見えて数値を良くすることができる点にある。
人は機械と違って無理がきくから、休憩もとらずどんどん動けば能率はあがる。また、5人で生産する工程で、現場の監督者が作業を手伝って6人で作業してラインストップを少なくしても、能率は上がる。こういうやり方を「見せかけの能率向上」というが、数字をあげるため現場がついつい手を染めたくなる手法である。
しかし、それをやって数字を良くしても、さらに数字を上げるためもっと働く、もっと手伝うという悪いサイクルにはまり、作業者は苦しむことになる。
人間というのは機械より無理がきき、結構頑張れるから、こういう悪いサイクルが知らぬ間に回ってしまっていることもある。「能率」だけを見ているとそういう罠にはまることになる。
「能率」に口を出す
昭和40年ころまでの生産基盤確立期にあっては、トヨタの生産台数は、年5割増しで伸び、現場が能率向上に励むことは生産台数の増大にも直結し、会社業績もどんどん伸びた。比例して給料も上がった。現場のモチベーションも上がった。
会社としても、この時期トヨタ生産方式の神髄であるジャストインタイム(JIT)を完成させるべく、必死であった。トヨタ生産方式の育ての親といえる大野耐一氏の指導の下、現場は日々、「カイゼン」を重ね、ジャストインタイムやかんばん方式が定着していき、現場にも力が付いてきた。
トヨタではジャストインタイムを実現するため、分かりやすい標語として「ムリ、ムダ、ムラを無くす」ということをいう。「ムリ」な作業は、不安全、不良につながる。「ムダ」な作業は能率を下げると同時に、作業者の首を絞めることにつながる。「ムラ」のある作業も、能率を下げるし、作業者は却って疲れる。作業はリズミカルに行われる方がいい、ということだ。
これが、額面通りに行われていれば、現場の作業者は、創意工夫、カイゼンを進めるたびに、楽になっていくはずだ。
しかし、人間というのは、時に限界を超えてまで頑張ってしまう。人間にはそれが可能であるからだ。人は機械より「強い」面がある。機械は「ムリ」を重ね過ぎれば「壊れる」。しかし人間は余程長くそれが続かない限り耐えてしまう。それが怖い。
現場に上がった悲鳴
昭和40年代に入り、現場からは、「『能率向上』に追いまくられる。」「もうくたくただ」「日曜日は寝ているしかない。」「班長がラインに入っている」というような声が出るようになった。
労働組合は、危機感をもった。とはいえ、それまで、「基準時間」の設定、「能率向上」は、トヨタにおける生産性向上運動の骨格であり、それは経営権の発露として実行されていることであるから、労働組合としては口を出すべきではないと、一種タブー視されていた。したがって、なかなか組合内部でも議論の輪が広がらなかった。しかし、そんなことを言っていては、トヨタ生産方式が従業員を苦しめる道具になってしまう。
この危機感から、タブーを破ったのは、その頃委員長として多くのトヨタ労組改革を成し遂げた梅村志郎委員長を筆頭とする、当時の組合三役陣だった。日々侃々諤々(かんかんがくがく)の議論を繰り返し、ついに、会社に、「基準時間」の決め方に、人としての余裕をいれること、あるいは能率向上を無限に要求しないことなどを申し入れたのだった。
会社がすぐにそれを容れてくれたわけではない。だが、昭和40年代から50年代に入り、労働組合は、直接それらの数字の設定に関わることはなかったにしても、本来作業に入るべきでないチームリーダーがラインで働くことがないよう運動するとか、年休の数字を監視し、それが急に悪化する部署は危ないとか、労働組合なりの着眼点で会社に危険信号を発し、数字の一人歩きや、見せかけの能率向上を防ぐようにした。
会社も徐々にではあるが、そのような視点を大事にしてくれるようになった。私が書記長の時代になると、会社との労使協議で、「基準時間」の設定のあり方に関し堂々と発言できるようになっていた。
年休のカットゼロ(完全取得)達成
トヨタ労組は10年ほど前に、ほぼ全職場で年休のカットゼロ(平均にすると17日くらい)を達成し、それを続けている。いまではトヨタでは、「年休カットゼロをできないような課長は失格だ」と言われるまでになった。
実は、これが可能になったはじめの一歩は、「能率」に労働組合が口を出し始めた30年前に遡るのだ。その歴史こそが、能率から言えば、「悪」ともいえるライン外要員の確保を会社に認めさせることを可能にした。ライン外要員が確保できなければ「年休カットゼロ」は絵に描いた餅になっていたであろう。
プライムコンサルタントでは、本記事のようにWEB会員限定サービスをご提供しています。
「WEB会員」サービスはどなたでも無料でご利用いただけます。
今すぐご登録ください(入会金・会費など一切無料です。また、ご不要であればいつでも退会できます)。